Refrigeration Recommendations
Refrigeration and cooling
Cooling on farms includes freezers, refrigerators, and evaporative coolers used to store farm products until distribution. The way farms meet their cooling demands ranges from small refrigerators (such as those found in a household), to larger units (such as a 6’x6′ or larger walk-in box) or units with a glass door for merchandising. The production of cooling equipment also varies, ranging from Energy Star-rated equipment to Do-It-Yourself evaporative cooling pads or walk-in coolers built with air conditioning units and Coolbot controllers.
While refrigeration technology on farms varies, refrigeration is a significant energy use and cost on most farms. There are ways to save energy on cooling that do not require large capital expenditures, and we recommend implementing those measures immediately for the reduced energy use and cost savings they offer. Other measures require significant capital expenditure and are best applied to areas where refrigeration operates for several months annually. Continue reading to learn more about specific energy-efficiency measures for refrigeration and cooling.
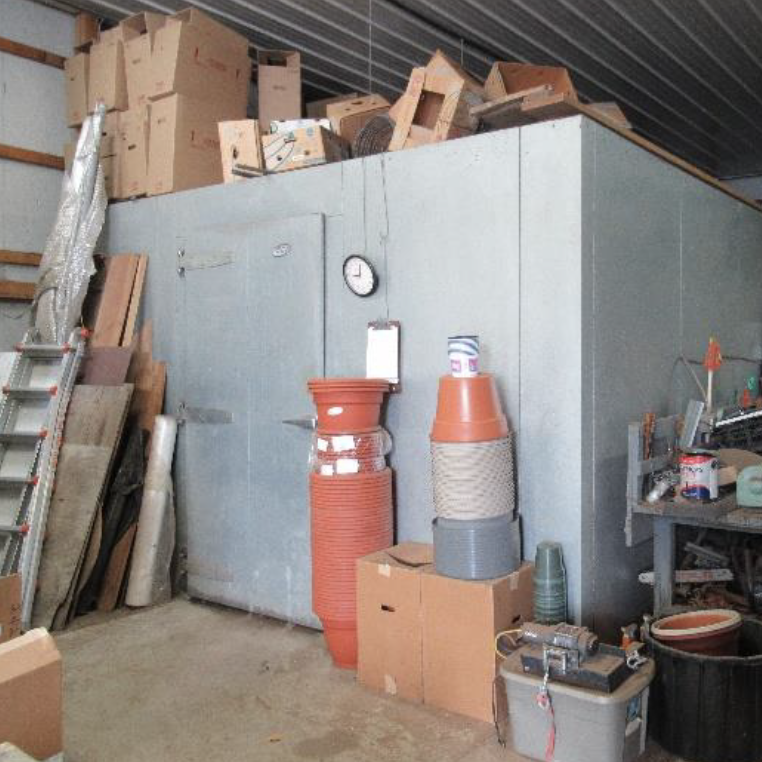
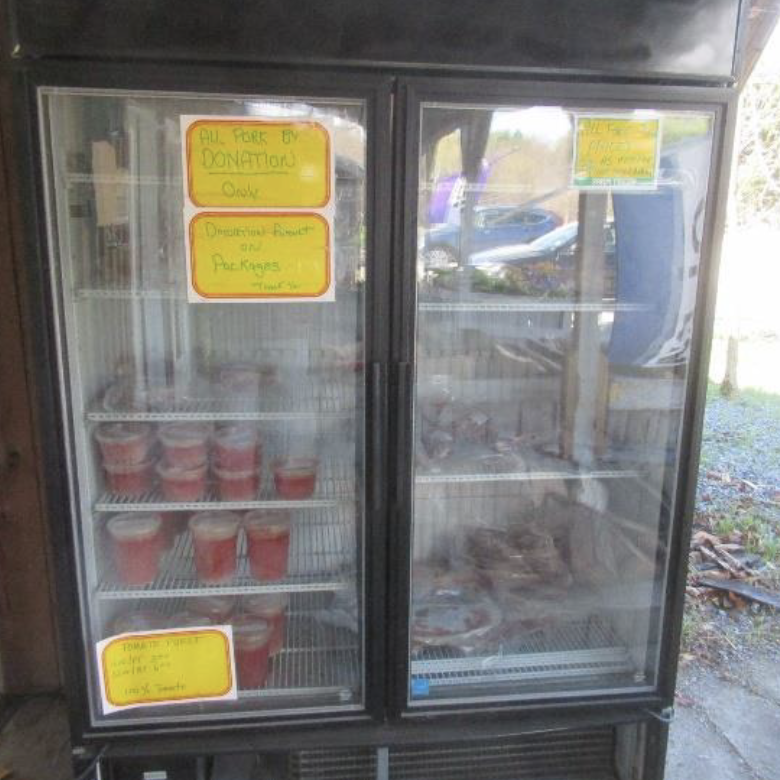
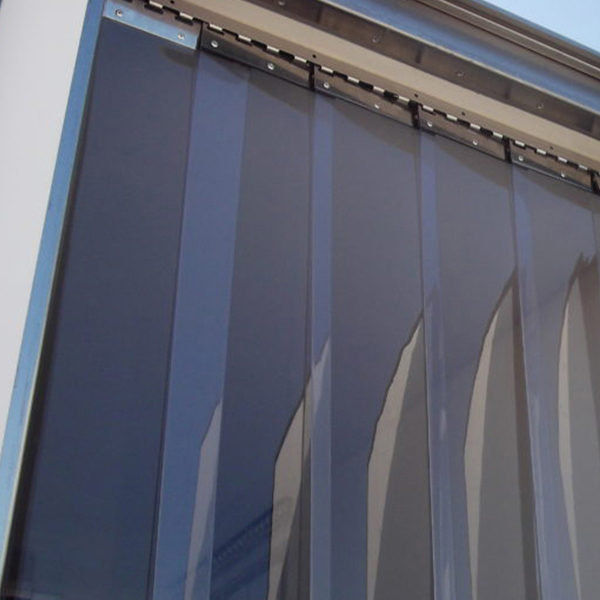
The measures below are listed from least to most costly in general, though costs vary depending on farm specifics. No-cost energy assessments can help you identify what measures are best suited for your operations considering costs and expected benefits. Request an energy assessment by completing our interest form.
Hidden First Toggle with No Content
Preventative Maintenance - Refrigeration Tune Up
Clean and inspect condenser coils • Clean and inspect evaporator coils • Clean drain pan • Clean and inspect fans • Clean or replace screens, grills, filters, and drier cores; tune the defrost cycles | |
Potential Energy Savings (1) | 1-5% |
Typical Simple Payback (2) | 1-3 years |
Possible Barriers | Equipment access (which should be corrected) |
Non-Energy Benefits | Avoiding premature equipment failure |
Industry Information and Resources |
|
1. “Potential Energy Savings” represents the potential savings as a percentage of the total energy use for each technology category. E.g., if “refrigeration” as an end-use was 20% of a farmer’s electricity usage, and if the above table showed a Potential Energy Savings of 25%, then the net effect would be a 5% overall electricity energy savings (20% * 25% = 5%). An individual farmer can then predict the Economic Benefit through annual cost savings by taking 5% of their annual bill. So, if a farmer’s annual electricity bill is $10,000 then the potential cost savings for implementing this example best practice would be 5% * $10,000 = $500.
2. “Simple Payback” is defined as the installation costs divided by the potential energy cost savings. An individual farmer can then predict the Expected Implementation Cost by taking the cost savings from item #1 above and multiplying it by the Simple Payback for the Technology being investigated. So, if the example best practice had a Typical Simple Payback of 3.0 years, then the estimated implementation cost would be $500 * 3.0 = $1,500.
Disconnect Defrost Heaters
Easy energy savings are available on some walk-in coolers operated at above-frezing temperatures:
Electric defrost systems use heating elements installed next to a refrigerator’s evaporator coils. These are used during defrost cycles to melt accumulated ice which would otherwise degrade refrigerator performance. The electrical heating elements are energized in defrost cycles and the refrigerator blows hot air around those elements over the evaporator coil to melt the ice.
If you use a walk-in cooler for refrigeration above freezing temperature, the built-in evaporator fans can melt the ice sufficiently. Disconnecting electric defrost systems will prevent them from becoming energized during the defrost cycle, avoiding unnecessary energy use and costs.
This measure only applies to coolers that operate with above-freezing temperatures both within the cooler and in surrounding air; in other cases, the system requires an electric defrost, or an energy-efficient alternative such as the hot gas defrost systems described below.
Strip Curtains
Consistently keeping the walk-in cooler doors closed is the best way to maintain desired temperature and moisture levels. Strip curtains can be installed as a low-cost measure to reduce energy loss when cooler doors are open.
Refrigeration Controls
Electronic controls of refrigeration components can precisely adjust compressor and fan operations in response to real-time conditions, to improve energy efficiency and overall system performance. Most refrigeration systems do not need advanced electronic controls to operate efficiently. However, complex systems with multiple compressors call for more elaborate refrigeration controls.
The images above show two types of refrigeration controls (a time-switch and a thermostat), and a compressor bank that could benefit from sophisticated controls.
Brushless Motors
Old and worn standard-efficiency motors should be replaced with high-efficiency options – the more hours a motor operates, the more cost-effective it is to replace it with a high-efficiency electronically commutated (EC) motor, also known as a brushless motor. Compared with standard brushed or induction motors, brushless motors use less raw materials to build, are less prone to mechanical failure, dissipate less heat, and are smaller and more energy efficient. These features make brushless motors better for the environment and long-term operations. Although the upfront cost may be more, the return on investment tends to be quick, especially for motors that run for many hours.
Scroll Compressors and Air Compressor Maintenance
In comparison with other types of compressors, scroll compressors are more efficient and less prone to mechanical failure since there are only two moving parts – a fixed and an orbital scroll. Scroll compressors can reach 100% volumetric efficiency and operate more smoothly and quietly because of the absence of gas compression pistons. Switch to scroll compressors when you need to replace or get a new compressor or refrigerator – scroll compressors save money by reducing energy use, while improving performance.
The tables below summarize information about getting the best results from your air compressors and from scroll compressors specifically.
Compressed Air OptimizationSetpoints should be close to 90 psi (110 psi max) if they are unnecessarily set higher. When multiple compressors are run in series, the lead-lag arrangements should be tuned to spread out wear-down on each unit and to optimize performance for all compressors in the arrangement. When base load is sufficient to warrant new purchases for compressor systems, variable speed compressors should be installed. |
|
General Operational Requirements | For farms with compressed air needs beyond general shop uses. |
Potential Energy Savings (1) | 5-30% |
Typical Simple Payback (2) | 1-7 years |
Possible Barriers | Cost; unique compressed air requirements. |
Non-Energy Benefits | Reduced wear and tear on the compressor. |
Industry Information and Resources |
1. “Potential Energy Savings” represents the potential savings as a percentage of the total energy use for each technology category. E.g., if “refrigeration” as an end-use was 20% of a farmer’s electricity usage, and if the above table showed a Potential Energy Savings of 25%, then the net effect would be a 5% overall electricity energy savings (20% * 25% = 5%). An individual farmer can then predict the Economic Benefit through annual cost savings by taking 5% of their annual bill. So, if a farmer’s annual electricity bill is $10,000 then the potential cost savings for implementing this example best practice would be 5% * $10,000 = $500.
2. “Simple Payback” is defined as the installation costs divided by the potential energy cost savings. An individual farmer can then predict the Expected Implementation Cost by taking the cost savings from item #1 above and multiplying it by the Simple Payback for the Technology being investigated. So, if the example best practice had a Typical Simple Payback of 3.0 years, then the estimated implementation cost would be $500 * 3.0 = $1,500.
Preventative Maintenance of Scroll CompressorsCheck, and adjust if needed: oil level, oil filter, and air inlet screen. See manuals of your specific units for more details. |
|
Potential Energy Savings (1) | 1-5% |
Typical Simple Payback (2) | 1-3 years |
Possible Barriers | Equipment access (which should be corrected). |
Non-Energy Benefits | Avoiding premature equipment failure. |
Industry Information and Resources |
1. “Potential Energy Savings” represents the potential savings as a percentage of the total energy use for each technology category. E.g., if “refrigeration” as an end-use was 20% of a farmer’s electricity usage, and if the above table showed a Potential Energy Savings of 25%, then the net effect would be a 5% overall electricity energy savings (20% * 25% = 5%). An individual farmer can then predict the Economic Benefit through annual cost savings by taking 5% of their annual bill. So, if a farmer’s annual electricity bill is $10,000 then the potential cost savings for implementing HE Refrigeration would be 5% * $10,000 = $500.
2. “Simple Payback” is defined as the installation costs divided by the potential energy cost savings. An individual farmer can then predict the Expected Implementation Cost by taking the cost savings from item #1 above and multiplying it by the Simple Payback for the Technology being investigated. So, if the HE Refrigeration had a Typical Simple Payback of 3.0 years, then the estimated implementation cost would be $500 * 3.0 = $1,500.
Install a Hot Gas Defrost System
When heating elements are needed for defrost cycles, hot gas defrost is a system that offers long-term energy savings once installed. Note that refrigeration systems operating in above-freezing temperatures may not need a defrost system (see Disconnect Defrost Heaters section above).
Hot gas defrost systems use heat from a refrigerator’s compressor to melt any frost on the evaporator coil. This defrost system consumes less energy than heating air with electric heating elements. Hot gas defrost also heats the entire evaporator coil, and only a small amount of that energy warms the refrigerated area, meaning the refrigerator has to do less work to stay cool through defrost cycles.
Hot gas defrost generates less moisture compared to electric defrost because the evaporator coil is heated using air already in the refrigeration system. Hot gas defrost also tends to have a shorter defrost time, because hot gas is immediately available from the compressor when the defrost cycle begins. Shorter defrost cycles help reduce temperature variations throughout a refrigerator’s operating cycles and also reduce strain on the compressor, improving the lifespan of refrigerator parts. Hot gas defrost uses more complicated piping and tends to be more costly to design and install. It is recommended that this technology be installed when replacing or expanding refrigeration systems.
Energy Star Refrigeration
Refrigerator and freezer energy use is affected by heat gain through freezer walls, heat infiltration through door seals, the efficiency of the evaporator fan motors and lighting, and operational inefficiencies due to dirty heat exchangers.
Modern ENERGY STAR-rated refrigerators and freezers have more insulation, improved controls, and improved fan, lighting, and coil technologies to minimize energy loss and consumption. According to the Environmental Protection Agency (EPA), ENERGY STAR-rated refrigerators and freezers are at least 30% more efficient than standard freezer models. When replacing equipment or expanding refrigerators and freezers, we recommend installing ENERGY STAR-rated units.
HE Refrigeration Summary
High efficiency (HE) refrigeration includes well-insulated walk-in, upright, and chest refrigerators/freezers that feature strip curtains, brushless motors, scroll compressors, and controls to adjust power based on temperature, humidity, air circulation, and any other important environmental variables. |
|
General Operational Requirements | Higher cost items such as HE refrigeration systems are most appropriate on farms that have cooling needs beyond only seasonal use. |
Potential Energy Savings (1) | 9-44% |
Typical Simple Payback (2) | 1-9 years |
Non-Energy Benefits | Improved produce quality |
Industry Information and References
Langston, D. 2011. The Case for a Refrigeration Preventative Maintenance Program. Aire Rite Air Conditioning and Refrigeration, Inc. Available at: https://cdn.ymaws.com/www.rfmaonline.com/resource/resmgr/rfma_conference_presentation_archives/the_case_for_a_refrigeration.pdf
Massachusetts Farm Energy Program (MFEP). 2012. Dairy Farms Best Practices: High Efficiency Refrigeration and Scroll Compressors. Massachusetts Department of Agricultural Resources, Amherst, MA. Pages 27-33. Available at https://massfarmenergy.com/wp-content/uploads/2014/03/Dairy%20Farms%20Best%20Practices.pdf
U.S. Department of Energy (DOE). 2003. Improving Compressed Air System Performance: A Sourcebook for Industry. Office of Energy Efficiency and Renewable Energy (EERE). Available at: https://www.energy.gov/sites/default/files/2014/05/f16/compressed_air_sourcebook.pdf
Wisconsin Department of Agriculture, Trade, and Consumer Protection (DATCP). 2006. Dairy Farm Energy Management Handbook. Madison, WI. Page 11. Available at: https://datcp.wi.gov/Documents/DAD/DairyFarmEnergyManagementHandbook.pdf
Wisconsin Focus on Energy. 2020. Energy Best Practices Guide: Agricultural Facilities. 2020. Madison, WI. Available at: https://www.focusonenergy.com/sites/default/files/inline-files/2020_Energy_Efficiency_Best_Practices_Guide-Agriculture.pdf
Wisconsin Focus on Energy. 2015. Technical Reference Manual. Madison, WI. Available at https://focusonenergy.com/sites/default/files/TRM%20Fall%202015%20_10-22-15.compressed2.pdf